EVERETT—Tens of thousands of International Association of Machinists (IAM) 751 & W24 union members returned to work Tuesday, November 12, following approval of a historic agreement with Boeing on November 4, ending a 53-day strike that cost the aerospace juggernaut billion dollars in lost revenue.
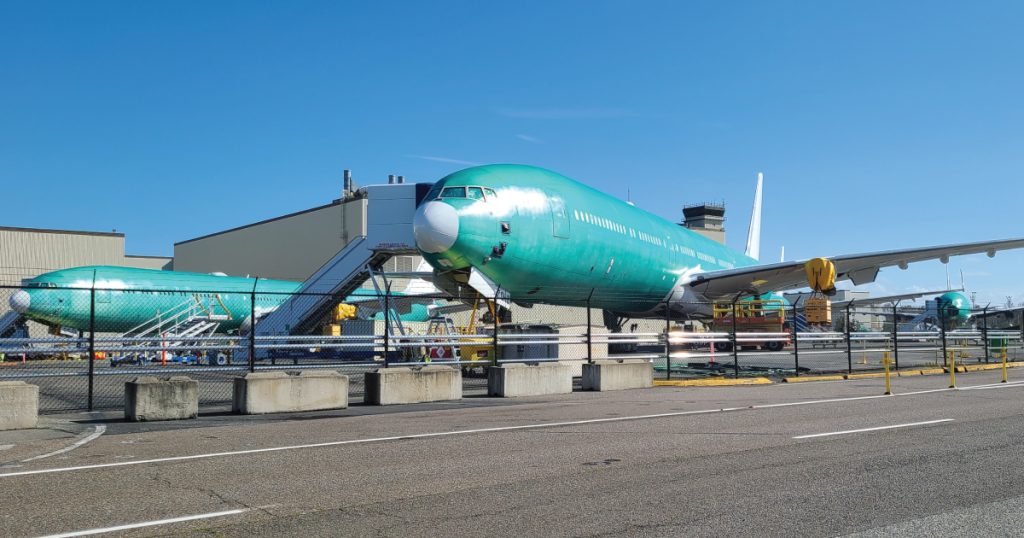
The Boeing Production System follows a lean methodology utilizing Just-in-Time, CONWIP, and Job Shop philosophies. Because of this complexity, it will be several weeks before Boeing will be at steady-state—full production—of its 737, 767, 777/777X and military derivatives P-8 and KC-46A aircrafts, a Boeing spokesman said.
For its ramp up plan, Boeing will continue to comply with its Safety Management System policies that include employee training and certifications.
Airplanes that have been completed and certified will continue to be delivered from the Everett and Seattle delivery centers, as well as Boeing South Carolina.
The Boeing spokesperson shared with the Lynnwood Times that CEO Kelly Ortberg’s four-point plan to “stabilize the business” is in full swing, which includes upcoming layoffs of approximately 17,000 employees or 10% of its workforce.
“As we’ve previously shared with our team, most affected U.S. employees will be notified mid-November and leave the company on January 17, 2025,” a Boeing spokesman said. “We are supporting these teammates with additional resources such as severance pay and career transition services.”
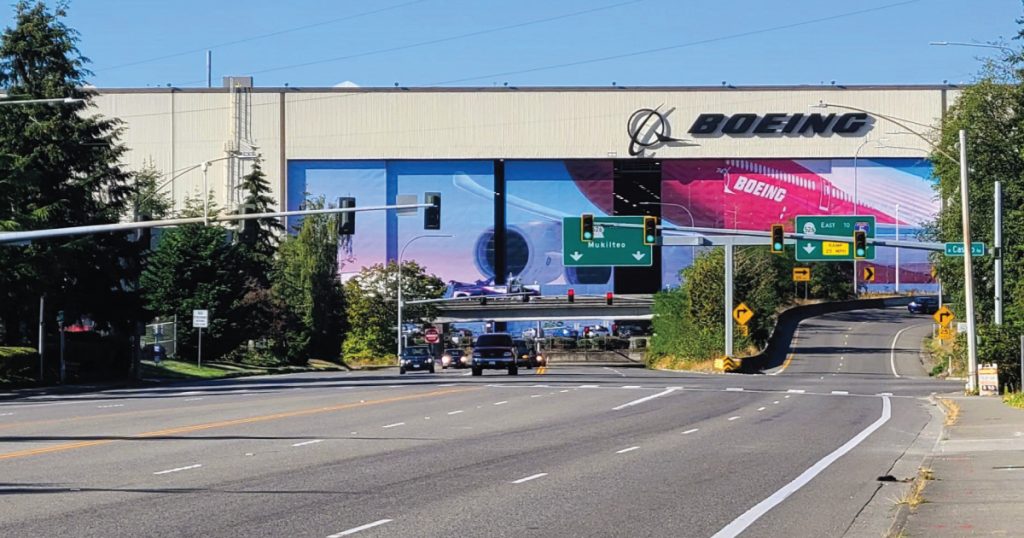
At its third-quarter 2024 earnings briefing on October 23, Boeing President and CEO Kelly Ortberg shared the grim reality of the company’s financial challenges ahead and his four-point plan to “restore Boeing to the leadership position that we all know and want.”
Ortberg framework is akin to Dr. W. Edwards Deming approaches to effective business management:
- Culture change
- Stabilize the business.
- Improve execution discipline on new platform commitments
- Build a new future
He also committed to a returned emphasis on core total quality management (TQM) principles to “prevent the festering of issues” and “identify, fix, and understand root cause[s].”
After machinist voted to approve an historic contract with Boeing in November 4, IAM 751 President Holden said at the presser that it is “time for us to come together” and clamed “victory.”
The average annual machinist pay at the end of this 4-year contract will be $119,309. This is an increase of about $43,700 from the previous contract’s $75,608 average. Below is a summary of key provisions in Monday’s approved contract:
- 38% General Wage Increase (up from 35% in 10/19 offer). This is an effective 43.65% wage increase.
- Year 1: 13%, Year 2: 9%, Year 3: 9%, Year 4: 7%
- $12,000 ratification bonus (up from $7,000 in 10/19 offer)
- Boeing 401(k) match increased to 100% of first 8% of pay, plus automatic 4% company contribution (80% of our employees max out their 401(k) contributions).
- Commitment to build Boeing’s next new airplane in the Puget Sound region.
- Annual bonus with 4% guaranteed annual payout, up to 6%.
- Retirement benefits also include:
- New 401(k) annuity option for guaranteed monthly retirement disbursement; Boeing pays the transaction fee.
- For employees with a Boeing pension (hired before Jan. 2014), offer increases pension multiplier from $95 per year of service to $105.
- For health care, 2025 paycheck contributions will be lower than 2024.
IAM workers could have return to work as early as the first shift on Wednesday, November 6, but today, all had to return no later than their beginning shift on November 12.

Author: Mario Lotmore
One Response
That’s what they preach but not what we’ve been doing for last 3-4 years.
“The Boeing Production System follows a lean methodology utilizing Just-in-Time, CONWIP, and Job Shop philosophies. Because of this complexity, it will be several weeks before Boeing will be at steady-state—full production—of its 737, 767, 777/777X and military derivatives P-8 and KC-46A aircrafts, a Boeing spokesman said.”